Chinese factories often face challenges with using the right materials in production. This issue can lead to serious consequences, affecting everything from product quality to brand reputation. Incorrect materials not only compromise the durability of your products but can also result in financial losses and damage to your trust with customers.
As a business owner, you need to be aware of how these mistakes can impact your operations. When factories use substandard materials, it not only affects the end product but also your brand’s image in the marketplace. Consumers expect reliable products, and any failure can lead to negative reviews and reduced sales.
This article will focus on identifying the problems caused by the use of incorrect materials, exploring how to resolve these issues, and providing strategies to prevent them in the future. You will gain insights that can help safeguard your business and maintain high standards in your production process.
Understanding the Issue: Wrong Materials in Manufacturing
Using the wrong materials in manufacturing means selecting or using substances that do not meet the required specifications. This can include:
- Substituting inferior materials for those specified
- Using materials that are mislabelled
- Failing to meet industry standards
Examples of these issues can occur when a factory uses a lower grade of steel instead of the designated type. This misstep can lead to structural failures that pose safety risks.
Early detection of wrong materials is critical. If you can identify these issues promptly, you can minimize financial losses and prevent potential accidents. Here are some key points to consider:
- Regular Inspections: Conduct frequent checks on material specifications.
- Quality Control Protocols: Implement strict guidelines to ensure materials meet the required standards.
- Staff Training: Educate employees about the importance of sourcing the right materials.
Chinese factories face challenges in sourcing proper materials and detecting errors. With improvements in quality control methods, these issues can be addressed effectively.
Awareness and proactive measures can lead to significant improvements in manufacturing processes, ultimately enhancing quality and reliability in your products. By knowing what to look for, you can protect your operations and ensure the safety of your final products.
Common Reasons for Using Wrong Materials
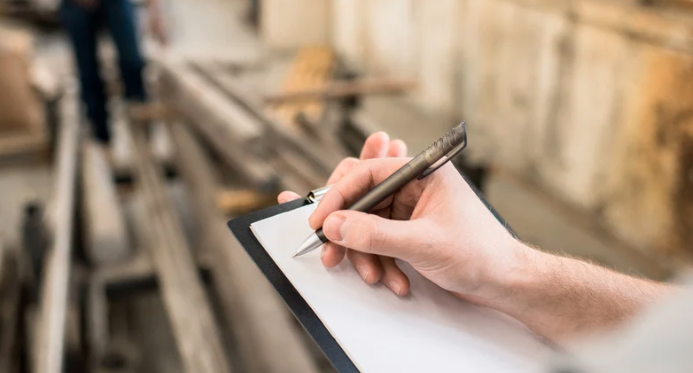
Several factors contribute to factories selecting incorrect materials for production. Understanding these reasons can help in preventing future issues and ensuring quality in manufacturing.
Cost-cutting Measures
Many factories aim to reduce their production costs. This can lead to using cheaper materials instead of those specified. For instance, a factory might substitute low-grade plastic for a stronger type to save money.
While this strategy can lower expenses, it often results in products that do not meet safety standards or durability requirements. If you’re sourcing from a factory, it’s vital to discuss your budget while also emphasizing the importance of quality to avoid such compromises.
Miscommunication or Misunderstanding of Specifications
Clear communication is essential in manufacturing. Sometimes, the specifications provided can be unclear or misunderstood by the factory staff. For example, a supplier might interpret "high strength" differently than intended.
Such discrepancies can lead to the use of inappropriate materials. To minimize this risk, ensure that you provide detailed specifications and engage in discussions to confirm understanding before production begins. Regular check-ins during the manufacturing process can also help clarify any doubts.
Lack of Quality Control
Quality control is crucial in ensuring that the right materials are used. Factories with poor quality control processes may not catch mistakes in material selection. For example, if an inspection team fails to identify the use of incorrect materials, the final product may not meet quality standards.
You should prioritize working with factories that have strong quality control protocols in place. Regular audits and inspections can help ensure compliance with material specifications, helping to avoid potential problems down the line.
Supplier Fraud
In some cases, suppliers may knowingly provide subpar materials instead of what was agreed upon. This fraud can occur when suppliers cut corners to maximize profit. For example, a supplier might pass off cheaper steel as premium quality steel.
You can mitigate the risk of supplier fraud by conducting thorough background checks and establishing strong relationships with your suppliers. It’s also wise to have testing and verification processes in place to ensure that the materials received meet the agreed-upon standards.
Also read: Scammed by a Chinese Supplier? Here’s How to Recover & Protect Your Business
Implications of Using Wrong Materials
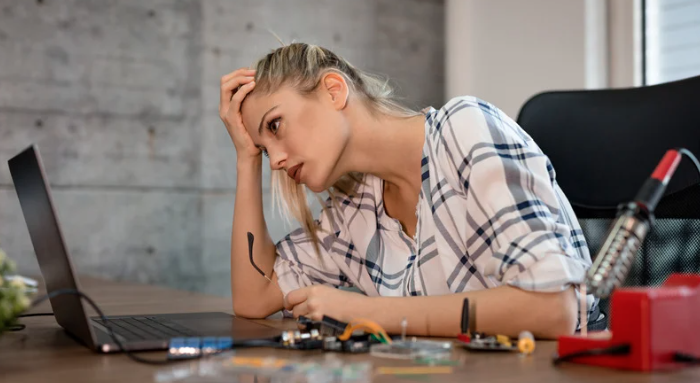
Using the wrong materials in production can lead to serious consequences for businesses. These issues can range from financial losses to damage to reputation, legal troubles, and a decline in customer trust. Each of these factors is critical for maintaining a successful operation.
Product Recalls and Financial Losses
When wrong materials are used, products might not meet safety standards. This can result in costly product recalls. A recall can lead to substantial financial losses due to the cost of retrieving the faulty products and compensating affected customers.
Additionally, there may be expenses associated with replacing the defective items. For example, the Mattel toy recall in 2007 cost millions and impacted their profits significantly. Handling a recall also takes time and resources away from other business activities.
Damage to Brand Reputation
Your brand's reputation can suffer greatly if customers associate it with inferior quality. If consumers receive products that fail to meet standards, they may spread negative reviews.
Consistent use of wrong materials compounds this issue. A damaged reputation is hard to repair and can lead to long-term effects on sales. Companies may spend years trying to rebuild trust in their brand, involving extensive marketing efforts and changes in quality control practices.
Legal Ramifications
Using inappropriate materials can result in legal troubles. If products cause harm due to poor materials, your company could face lawsuits or fines.
Regulatory bodies may also impose penalties if safety standards are violated. It is essential to follow proper guidelines to avoid legal issues that can arise from negligence. Such legal matters can drain resources and distract management from core business operations.
Customer Dissatisfaction and Loss of Trust in Chinese Goods
Customers may become dissatisfied if they receive products made from the wrong materials. This dissatisfaction can lead to lost sales and customer loyalty.
Over time, if customers experience repeated issues with quality, they may begin to distrust products from your company and even the broader market. Building customer trust takes significant effort while losing it can happen in an instant.
To combat this, transparent communication about materials and quality assurance processes is vital in keeping your customer base engaged.
How to Prevent the Use of Wrong Materials?
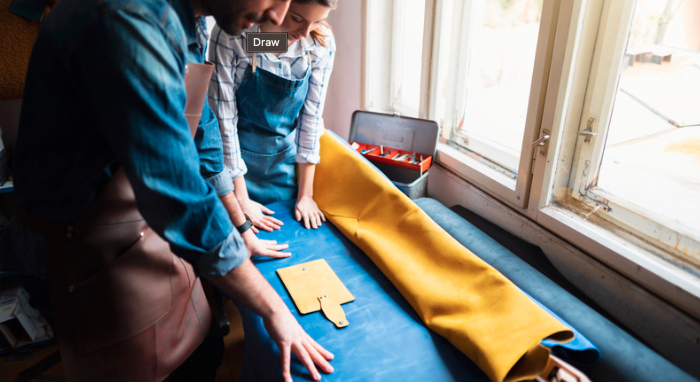
Preventing the use of wrong materials in manufacturing requires a focused approach. Implementing proper supplier management, creating detailed product specifications, conducting regular inspections, and using third-party verification services are essential steps to ensure quality.
Vetting and Selecting Reliable Suppliers
Choosing the right suppliers is crucial for maintaining quality in your materials. Start by researching potential suppliers thoroughly. Look for companies with a strong track record, positive reviews, and relevant certifications.
Consider their production processes and how they ensure quality. Request samples to evaluate the material. Establish clear communication channels to discuss your specific needs. It's important to build relationships with suppliers who demonstrate reliability and transparency. Regularly review their performance to ensure they continue to meet your standards.
Clear and Detailed Product Specifications
Creating clear and detailed product specifications can significantly reduce errors. Document exact material requirements, including technical properties, dimensions, and tolerances.
Use diagrams or images where possible to illustrate your specifications. Make sure all relevant stakeholders understand these guidelines. Share specifications with your suppliers and verify their understanding before production starts. Regularly update specifications as needed to reflect changes in design or standards. Clarity is key in preventing misunderstandings that could lead to errors in materials.
Regular Quality Control Inspections
Implementing a robust quality control system is essential. Schedule regular inspections of incoming materials to check for compliance with your specifications. Use a checklist to evaluate key factors like material type, quality, and certifications.
Keep detailed records of these inspections to track supplier performance over time. If discrepancies arise, address them immediately with the supplier to prevent further issues.
Consider using sampling methods that allow you to monitor materials throughout production, ensuring quality is maintained at every step.
Use of Third-party Verification Services
Employing third-party verification services can add an extra layer of security in your supply chain. These services provide independent assessments of suppliers and their materials.
They can perform audits and inspections, ensuring that materials meet your specifications before they arrive at your factory. Look for reputable companies that specialize in quality assurance and compliance.
This not only helps you verify materials but also builds trust with your suppliers, knowing that they are held to high standards. Investing in these services can reduce the risk of using incorrect materials significantly.
Steps to Take When Wrong Materials Are Discovered
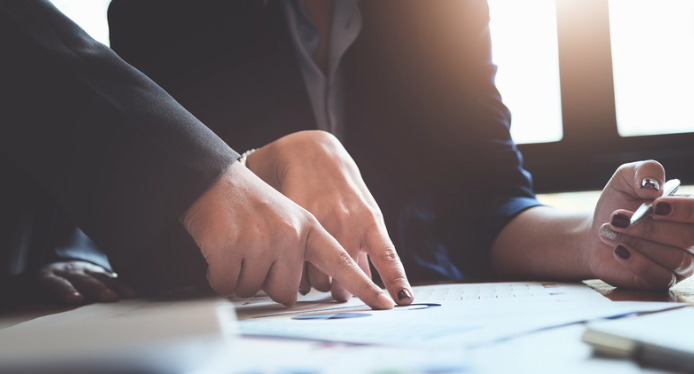
Discovering the wrong materials can disrupt your project and lead to unnecessary costs. Knowing how to address the situation is crucial. Here’s what you should do.
1. Immediate Inspection and Documentation
As soon as you identify incorrect materials, perform an immediate inspection. Check the materials against your order specifications. Look for any visible defects or discrepancies.
Next, document everything. Take clear photographs of the materials, showing their labeling and any defects. Keep a detailed record of when and how the mistake was discovered. This documentation will be essential for further steps.
Gather any relevant paperwork, such as purchase orders and delivery receipts. This ensures you have all the needed information at hand when you reach out to the supplier.
2. Contacting the Supplier With Detailed Complaints
Once you have assessed and documented the situation, contact your supplier. Be clear and concise about the issue. Provide them with the relevant details, including order numbers and dates.
Explain the specific problems with the materials. Include the documentation you gathered. This evidence strengthens your complaint and clarifies the issue.
Maintain a professional tone during communication. It's important to establish an open line for resolution. Make sure to request a timeline for their response so that you can plan the next steps accordingly.
3. Negotiating Replacements or Compensation
After contacting the supplier, be prepared to negotiate. Discuss possible replacements for the incorrect materials. Specify what you need and the urgency of the situation.
If replacements are not feasible, talk about compensation. This could include price adjustments, refunds, or any other terms that may help mitigate your losses.
Keep records of all communications for reference. This will be useful if you need to escalate the issue later. Aim for a solution that works for both parties while ensuring your project stays on track.
4. Legal Action and Dispute Resolution
If negotiations fail, consider legal options. Review your contract for clauses related to disputes. Understanding your rights can guide your next steps.
You may need to send a formal demand letter outlining your complaint. Include all supporting documentation. This letter should clearly state the expected outcome.
If the situation does not resolve, alternative dispute resolution methods, like mediation or arbitration, could be options before heading to court.
Legal action can be time-consuming and costly, so weigh your options carefully to determine the most effective path for your case.
Also read: Types of Lawyers in China
Conclusion
Addressing the issue of a Chinese factory using the wrong materials involves immediate action: verifying the discrepancy, documenting evidence, and communicating directly with the supplier to seek a resolution.
It's essential to review your contract terms and consider implementing stricter quality control measures to prevent future occurrences. Navigating such challenges can be complex, especially in international trade.
For professional legal advice and to ensure your rights are protected, consult Choi & Partners. Their expertise in international trade law can help you effectively manage disputes and safeguard your business interests.
Contact Choi & Partners today for comprehensive legal support.
Must Read Articles 📖:
- China Working Conditions Overview
- Scammed by a Chinese Supplier? Here’s How to Recover & Protect Your Business
Frequently Asked Questions
This section addresses common inquiries regarding the conditions in Chinese factories and the quality of the products they produce. You will find answers about human rights, treatment of workers, quality control, and the reasons behind the pricing of goods made in China.
What are the human rights violations in Chinese factories?
Human rights violations in Chinese factories can include long working hours, low wages, and poor working conditions. Reports indicate that some factories do not comply with labor laws, leading to exploitation and unsafe environments for workers.
What are the negative impacts of manufacturing in China?
Manufacturing in China can lead to environmental issues due to pollution from factories. There are also concerns about the social impact, such as the displacement of local communities and the prioritization of profit over worker welfare.
How are Chinese factory workers treated?
Chinese factory workers often face rigorous production demands and may endure harsh conditions. Some reports indicate that there can be limited rights or protections for workers, affecting their treatment and job security within the industry.
Does China have good quality control?
China's quality control practices vary by factory. While some factories maintain high standards, others lack proper documentation and oversight. Problems can arise when the production does not match samples due to differences in materials or methods.
Why are China products so cheap?
Products made in China are often cheaper due to lower labor costs and economies of scale. Many factories operate with reduced overhead costs, allowing them to sell goods at lower prices compared to other countries.
Subscribe to receive updates
Subscribe to receive the latest blog posts to your inbox every week.
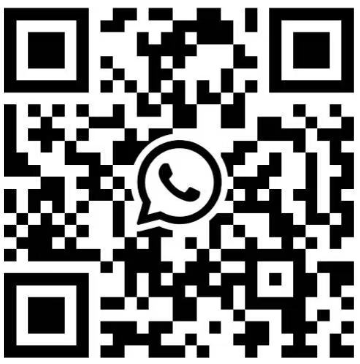